Sweet Home Alabama: GE Aviation to build unique materials factories in Huntsville
June 20, 2016
In a ceremony in Huntsville, Alabama on June 16, with Alabama public officials, GE Aviation broke ground on two adjacent factories to mass-produce silicon carbide (SiC) materials used to manufacture ceramic matrix composite components (CMCs) for jet engines and land-based gas turbines for electric power.
GE Aviation is investing more than $200 million to construct two factories on 100 acres in Huntsville. When the factories are fully operational later this decade, they are expected to employ up to 300 people. The plants are expected to be completed by the first half of 2018, with production set to begin the same year. GE expects to begin hiring the hourly workforce later this year.
One of the Huntsville plants (there will be two buildings) will produce silicon carbide (SiC) ceramic fiber. It will be the first such operation in the United States. Today, the only large-scale SiC ceramic fiber factory in the world is operated by NGS Advanced Fibers in Japan, which is a joint company of Nippon Carbon, GE, and Safran of France.
The second factory will use this SiC ceramic fiber to produce the unidirectional CMC tape necessary to fabricate CMC components.
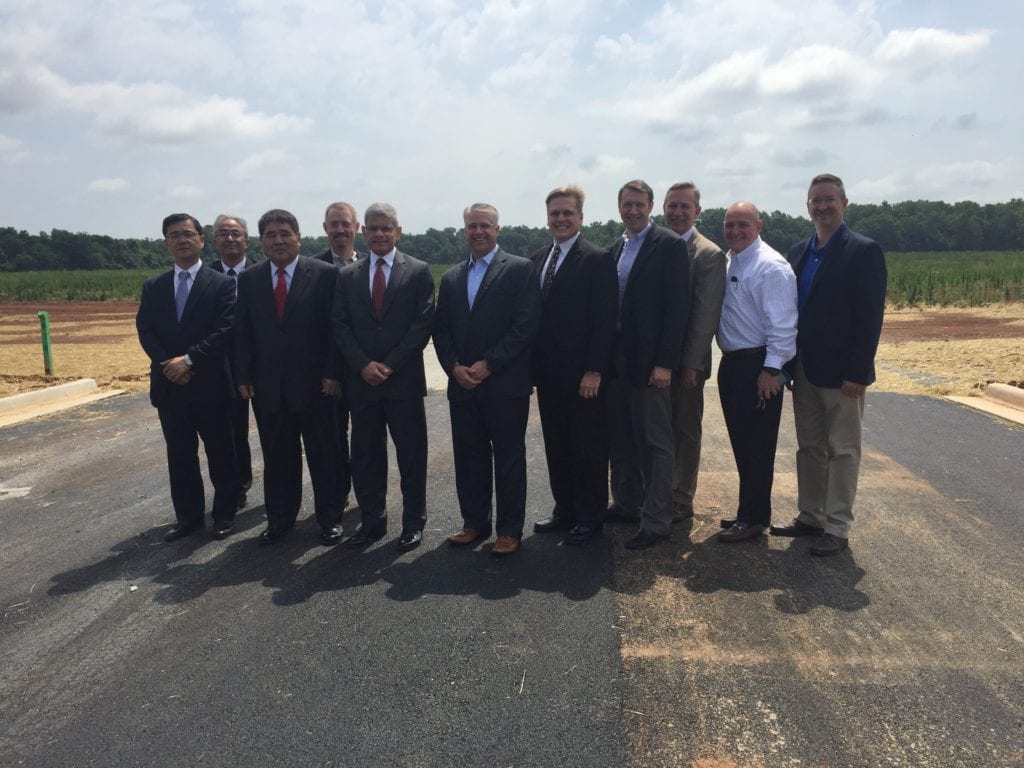
An advanced materials revolution in jet propulsion
The use of lightweight, heat-resistant CMCs in the hot section of GE jet engines is a breakthrough for the jet propulsion industry. CMCs comprise SiC ceramic fibers in a SiC matrix, enhanced by proprietary coatings. Check out this video about GE Aviation’s advancements in the Ceramic Matrix Composite Revolution.
With one-third the density of metal alloys, these ultra-lightweight CMCs reduce the overall engine weight. Further, their high-temperature properties greatly enhance engine performance, durability, and fuel economy. CMCs are far more heat resistant than metal alloys, hence requiring less cooling air in the engine’s hot section. By using this air instead in the engine flow path, an engine runs more efficiently.
For more than 20 years, scientists at GE’s Global Research Centers and GE’s industrial businesses have worked to develop CMCs for commercial applications. The best-selling LEAP engine, being developed by CFM International, the 50/50 joint company of GE and Safran Aircraft Engines of France, is the first commercial jet engine to use CMCs in the high-pressure turbine section. The LEAP engine, with more than 10,500 orders and commitments, is currently completing certification testing. It is scheduled to enter airline service next year powering the Airbus A320neo, and in 2017 powering the Boeing 737 MAX.
Rising GE Demand for CMC Components
The demand for CMCs is expected to grow tenfold over the next decade. Each LEAP has 18 CMC turbine shrouds, which are stationary parts in the high-pressure turbine that direct air and ensure turbine blade efficiency. Also, CMCs are being used in the combustor and high-pressure turbine section of the new GE9X engine under development for the Boeing 777X twin-aisle aircraft. More than 700 GE9X engines are on order today, with the aircraft entering service by 2020.
GE is incorporating CMC components in advanced military engines including the GE3000 for the U.S. Army’s ITEP program. GE’s advanced turboshaft demonstrator FATE (Future Affordable Turbine Engine) also for the Army increases the use of hot-section CMCs to achieve aggressive fuel efficiency, power-to-weight ratio, and lower maintenance cost goals. CMCs are currently being evaluated for upgrades to existing engines like the highly popular T700 helicopter engine.
https://www.youtube.com/watch?v=is1BBilkyUM
GE Aviation is investing more than $200 million to construct two factories on 100 acres in Huntsville. When the factories are fully operational later this decade, they are expected to employ up to 300 people. The plants are expected to be completed by the first half of 2018, with production set to begin the same year. GE expects to begin hiring the hourly workforce later this year.
“GE Aviation is creating a fully integrated supply chain for producing CMC components in large volume, which is unique to the United States,” said Sanjay Correa, Vice President who leads the industrialization of advanced technologies at GE Aviation. “The new factories in Alabama are vital to this strategy.”
One of the Huntsville plants (there will be two buildings) will produce silicon carbide (SiC) ceramic fiber. It will be the first such operation in the United States. Today, the only large-scale SiC ceramic fiber factory in the world is operated by NGS Advanced Fibers in Japan, which is a joint company of Nippon Carbon, GE, and Safran of France.
The second factory will use this SiC ceramic fiber to produce the unidirectional CMC tape necessary to fabricate CMC components.
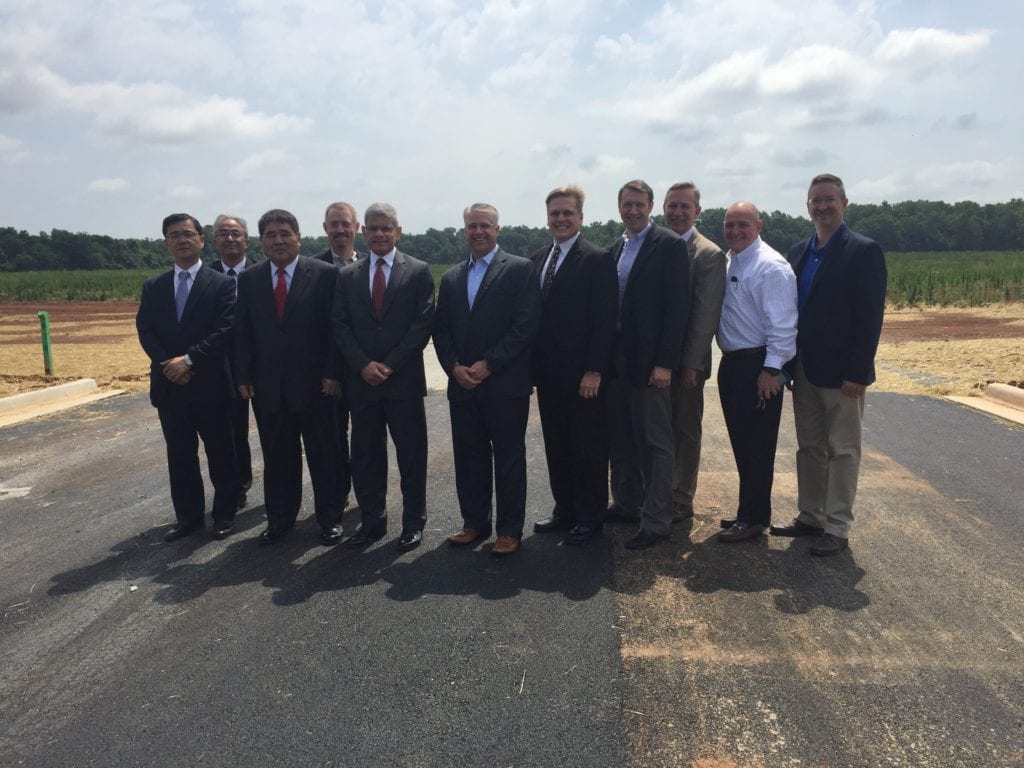
An advanced materials revolution in jet propulsion
The use of lightweight, heat-resistant CMCs in the hot section of GE jet engines is a breakthrough for the jet propulsion industry. CMCs comprise SiC ceramic fibers in a SiC matrix, enhanced by proprietary coatings. Check out this video about GE Aviation’s advancements in the Ceramic Matrix Composite Revolution.
With one-third the density of metal alloys, these ultra-lightweight CMCs reduce the overall engine weight. Further, their high-temperature properties greatly enhance engine performance, durability, and fuel economy. CMCs are far more heat resistant than metal alloys, hence requiring less cooling air in the engine’s hot section. By using this air instead in the engine flow path, an engine runs more efficiently.
For more than 20 years, scientists at GE’s Global Research Centers and GE’s industrial businesses have worked to develop CMCs for commercial applications. The best-selling LEAP engine, being developed by CFM International, the 50/50 joint company of GE and Safran Aircraft Engines of France, is the first commercial jet engine to use CMCs in the high-pressure turbine section. The LEAP engine, with more than 10,500 orders and commitments, is currently completing certification testing. It is scheduled to enter airline service next year powering the Airbus A320neo, and in 2017 powering the Boeing 737 MAX.
Rising GE Demand for CMC Components
The demand for CMCs is expected to grow tenfold over the next decade. Each LEAP has 18 CMC turbine shrouds, which are stationary parts in the high-pressure turbine that direct air and ensure turbine blade efficiency. Also, CMCs are being used in the combustor and high-pressure turbine section of the new GE9X engine under development for the Boeing 777X twin-aisle aircraft. More than 700 GE9X engines are on order today, with the aircraft entering service by 2020.
GE is incorporating CMC components in advanced military engines including the GE3000 for the U.S. Army’s ITEP program. GE’s advanced turboshaft demonstrator FATE (Future Affordable Turbine Engine) also for the Army increases the use of hot-section CMCs to achieve aggressive fuel efficiency, power-to-weight ratio, and lower maintenance cost goals. CMCs are currently being evaluated for upgrades to existing engines like the highly popular T700 helicopter engine.
https://www.youtube.com/watch?v=is1BBilkyUM