Every Part Is Its Own Puzzle: How Award-Winning Inspection Technology Helped Nicole Tibbetts Fall in Love with Services
March 14, 2024 | by Jay Stowe
When Nicole Tibbetts attended the 66th annual Laureate Awards in Washington, D.C., on March 14 to accept an award in the MRO category for GE Aerospace’s latest investments in engine inspection technology, she reluctantly bowed to tradition and wore a dress. Granted, the 14 other team members attending the awards ceremony at the National Building Museum wore tuxes. But anyone who works with Tibbetts, the chief manufacturing engineer for MRO (maintenance, repair, and overhaul) at GE Aerospace, knows this was a significant concession. On any given day, whether at her desk or checking in on one of the 18 MRO shops the company operates around the globe, she typically dresses to impress the shop floor — jeans, steel-toed work boots, long-sleeve shirts, half-zip microfleece tops, and safety goggles.
“If you don’t find me in my office, or if I’m having a bad day, I’ll go over to ACSC [Aviation Component Services Cincinnati], where you’ll find me cleaning parts,” she says. “I love working on the shop floor.”
Which makes a lot of sense, because part of Tibbetts’ job is to oversee the inspection technology that the company employs to ensure that its engines are in the safest working order possible. The Laureate Awards have singled out three advanced inspection technologies developed by GE Aerospace for “improving the efficiency, accuracy, and quality of inspections”: ultrasonic immersion, the artificial intelligence-enabled Blade Inspection Tool (BIT), and the Soft ElectroNics Skin-Innervated Robotic Worm (aka Sensiworm). Each one represents a “big investment that GE Aerospace has made in digitizing and automating inspection,” says Tibbetts. “What’s really unique about this humbling award is that it’s recognizing three different categories of innovation in inspection.”
Ultrasonic frequencies are above the range of human hearing. In nature, dolphins and bats use echolocation — sending out sound waves and listening for echoes that bounce back — to find food or evade an obstacle. At Aerospace Inspection Solutions (AIS) in Springdale, Ohio, GE Aerospace engineers take engine parts that have been exposed to thousands of hours of use and extreme temperatures, submerge them in large glass tanks of water, pulse the material with high-frequency sound waves, and analyze the sound reflections to look for flaws or anomalies that could be hiding inside the parts.
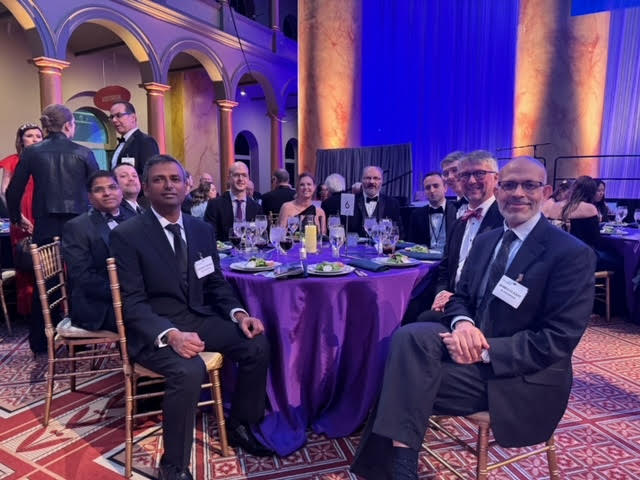
When the company started investing heavily in ultrasonic immersion technology in 2019, “that was really an investment in proactive safety,” says Tibbetts. “The idea was that we add additional inspection capability to field-run hardware.” Now the technology can be used not just in the lab at AIS but in the company’s MRO shops, as well as a bevy of third-party overhaul shops and non-destructive testing sites that the company has partnered with. Tibbetts describes it as a “safety framework.” “This is really something that we wanted to do to support our product and service globally, whether that work is done within our four walls or not,” she says.
The BIT tool was developed by Bristol Robotic Services, a GE Aerospace company based in the U.K., to inspect the stage 1 and stage 2 high-pressure turbine (HPT) blades in GEnx-1B and -2B engines. The device, which is equipped with an AI-enabled camera, can anchor into position and capture images that can be extracted and reviewed. It can also count and index each blade as it rotates into view — a very helpful advantage when you have to inspect more than 70 blades inside a GEnx HPT turbine.
“You’re always viewing the blade in the same way,” says Tibbetts. This enables technicians to compare and measure what they’re seeing — a crack, say, or a missing patch of thermal barrier coating — against a standard to determine if a blade is serviceable or non-serviceable. “It gives you a lot of objective measurement data against a subjective inspection,” she says. “The BIT tool is great because it actually creates an archive of the evolution of the hardware and service through time.” That kind of data provides “a much better predictive capability for when the engine needs to be removed,” she adds. “That’s great for the customer, because we avoid unplanned engine removals. And it’s great for product safety, because you can better avoid in-flight shutdowns.”
The BIT tool saves time, too. It takes only an hour and a half to run, whereas a session with a borescope, one of the most common tools used in MRO shops today, takes about three hours. Plans are in place to use the BIT tool to service the “maverick blade,” the next generation of the HPT stage 1 blade for the CFM LEAP engine, when it goes into service later this year. (CFM International is a 50-50 joint company between GE Aerospace and Safran Aircraft Engines.)
Sensiworm, the last of the three new technologies being honored, is still in the research phase at GE Aerospace’s Research headquarters in Niskayuna, New York. But it heralds advances that embody “the next 30 years of technology,” says Tibbetts. First off, it’s untethered, unlike a borescope, which has to be manually snaked into a jet engine and retrieved without getting stuck. The Sensiworm is autonomous; it propels itself by gripping surfaces and maneuvering into and through tight spaces that a borescope may not be able to get to. Second, the Sensiworm’s electronic skin is highly sensitive, allowing it to see and feel the surfaces it moves along and detect defects and corrosion, and even measure the thickness of thermal barrier coatings. “In terms of sensing technology, a borescope is just a light in the camera,” says Tibbetts. “You’re looking for visual data. Sensiworm has the opportunity to host other types of modalities of inspection.”
Of course, the need for new inspection technologies never rests. Tibbetts and her team are already trying out a non-destructive chemical testing technique called X-ray fluorescence to map the surfaces of engine parts and provide a full spectral analysis of their chemical composition. And by the end of the year she’s hoping to roll out a module-level ultrasonic probe to the company’s MRO network, enabling technicians to conduct on-the-spot ultrasonic inspections of HPT rotors in the CFM LEAP.
Tibbetts got her start in academia, where she completed a Ph.D. in long-lived radionucleotide chemistry. Even though she started working in chemical engineering at the GE Research Center when she first joined the company in 2010, the theory and practice of aviation services technology was not as big a leap as it may seem.
“I love working in services,” she says, “because every engine that comes in, every part that comes out, has a new problem to solve. It’s its own unique puzzle. I worked on long-lived radionucleotides because I liked the history of the earth and rocks. So there’s just something interesting to me about working on the history of something. And then the collaboration on the shop floor around the globe is really fun. No day is the same as the next.”