What’s in a Name? Now Fully Certified, the Catalyst Engine Is Ready to Transform the Future of Turboprop Flight
April 28, 2025 | by Chris Norris
In late February, some 800 engineers from five countries reached a major milestone in a journey most of them began nine years ago: The Catalyst engine, GE Aerospace and Avio Aero’s clean-sheet design for the most advanced turboprop engine of the 21st century, received its certification from the Federal Aviation Administration. Designed, developed, and made in Europe by Avio Aero, the Italian subsidiary of GE Aerospace, the engine will enter service on the Beechcraft Denali, a new midsize single-engine turboprop plane designed by Textron Aviation. But as its name suggests, its technology augurs changes throughout the aviation world.
“This was a huge team effort,” says Paul Corkery, who has served as the general manager of the Catalyst program since 2016. “We tapped our teams in Italy, Poland, Germany, and the Czech Republic, each of which had different skill sets, all of them driven by the call to develop a new centerline technology in a new-size package.”
A centerline, or “clean sheet,” design, is one that’s executed afresh from top to bottom, without using known components or reiterating existing products. “It means taking a blank sheet of paper and developing a whole engine from scratch,” Corkery explains. And it’s not undertaken lightly. “The reason you don’t hear much about clean-sheet [designs] is that they’re very demanding,” he says. “They’re complicated, expensive, and require intensive certification.” In this case, that meant 23 engine-level tests and more than 190 component-level tests, with 43 separate running engines completing 8,000 operating hours, 3,000 of them in flight.
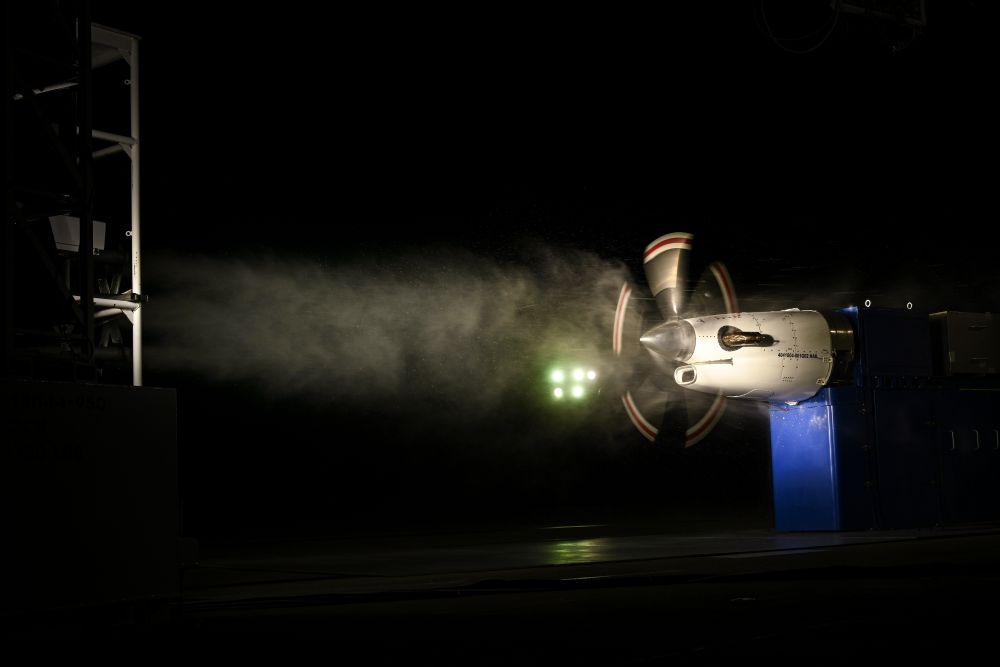
Fortunately, clean-sheet designs have a galvanizing effect all their own. “I grew up in engineering, and you don’t often get a chance to go in knowing you’ll actually change the market,” says Corkery. “Here, you’re working with the latest materials, on the latest airflow, compressor, and combustor technology. It’s the kind of thing that really gets engineers rolling. Being part of a clean sheet is kind of the apex of your engineering career.”
FADEC: Automatic vs. Stick Shift
The process began in 2016. “And right at the beginning, we set some very aggressive performance targets,” Corkery says: “15% better fuel burn than you see in today’s market, 10% more power as you got up in altitude.” And perhaps most striking, a design that integrates FADEC, or Full Authority Digital Engine Control, into the engine itself.
Previously exclusive to passenger jets, FADEC’s computer-based system manages engine parameters like fuel flow, torque, ignition timing, speed, and thrust — replacing the complex set of hydro-mechanical controls that are in most prop aircraft with a single lever. “This gives the pilot a jetlike experience,” Corkery explains. “The instruments know the condition the aircraft’s in and automatically optimize fuel schedule, prop schedules. It’s automatic versus stick shift, and something this market has never seen until now.”
This was part of a larger effort to bring contemporary jet technology to a new market. “We looked at what you see on large commercial aircraft,” Corkery relates. “We looked from right to left — from the compressor technology to the combustor technology to the turbine technology to the FADEC — and we said, ‘How can we hit these challenging performance metrics and bring this technology to a small package?’”
For the compressor, they would use two stages of “variable,” or moving, geometry to enable the engine to run at a pressure ratio significantly higher than any others in its class. New materials would allow the combustor to run significantly hotter than other engines, while an array of tiny holes in the turbine would cool the combustor and a secondary stage would harvest additional energy with aero mechanics.
Tapping into a Legacy of Innovation
While it pushes the envelope in several spheres of aviation, the Catalyst engine’s turboprop design actually goes back to the roots of GE Aerospace, which came into being as a producer of turbosuperchargers for B-17 engines during World War II. It was also during that war that the U.S. government sponsored the company’s top-secret development of America’s first jet engine.
The Catalyst engine program marshals this legacy to redefine the turboprop as a key component in the future of flight. And as it had been decades since breakthrough technologies were envisioned in a turboprop, Corkery says, “we saw an opportunity to drive technology into this market segment and to bring big-engine technology into a small package.”
The Catalyst engine is the first modern turboprop engine made with 3D-printed parts. What’s more, its innovative technologies and materials also make it the ideal architecture for developing more sustainable propulsive solutions through the European Union’s past Clean Sky 2 public-private partnership and its current Clean Aviation hybrid electric project AMBER, led by Avio Aero.
“If you look at the efficiency that we’re bringing, the reduced emissions, and FADEC’s ability to simplify, you see that we’re positioned well for hybrid solutions and architectures, no matter where they go,” says Corkery. “In the shorter term, you have hybrid solutions with battery architectures. In the slightly longer term, you have hydrogen-fuel-cell-based architectures. We’re positioned for either one.”
This is where this engine becomes a true change agent. “It’s going through that next sequence where the technology starts to move up — whether it’s in fuel burn, hybrid architectures, or wherever else it needs to go,” Corkery says. “We knew that the completion of the Catalyst engine would only be the beginning of the journey we wanted to enable. After all, that’s why we chose its name.”