The Real Deal: GE Aerospace’s XA100 Campaign Lays the Foundation for Next-Gen Engines
April 24, 2025 | by Cole Massie
Inside GE Aerospace’s sprawling headquarters campus outside Cincinnati, Ohio, engine parts of all shapes and sizes are neatly organized and categorized, filling up a secure room. It’s a standard practice anytime a new jet engine is developed and tested — you build it, test it, and take it apart.
The purpose of the exercise is to allow the engineers to perform an in-depth analysis on each piece of hardware they designed. They watched their hardware produce mountains of promising performance data during testing, but does the state of the physical part match it?
That’s what the team behind the XA100 — the world’s first flight-weight, three-stream adaptive cycle engine — is in this room to figure out. They want future engine designs to leverage everything they’ve learned from the years-long, high-intensity XA100 test campaign they wrapped up in June 2024.
Leading the disassembly effort is Mary Comer, the XA100's program leader, who also led the team through testing. She’s no stranger to testing new engines. In fact, the XA100 is her ninth new production introduction program with GE.
Established through the Adaptive Engine Transition Program (AETP), the XA100 program was founded to meet the challenge posed by the U.S. Air Force to the jet propulsion industry to produce the next generation of fighter engines. The goal was clear: enable fighters of the future to go further and faster while carrying increasingly advanced electronics and systems.
The “adaptive” moniker comes from the engine’s ability to adapt its airflow to deliver both high-speed performance and fuel-efficient cruising based on the pilot’s situation and throttle inputs. The technology has been in the works for nearly two decades and is a true differentiator for the United States as defense priorities call for longer-range missions.
“We didn’t find surprises, and that’s what you want,” Comer said following the disassembly process. “When your data matches what you see with the hardware after you take everything apart, it means you had a great test campaign.”
Running the Gauntlet
The test campaign for the XA100 program was especially unique. Not only was it the first AETP engine to be tested, but it also employed advanced technology never fully incorporated in a fighter engine design. Heat exchangers built using additive technology, rotating ceramic matrix composite parts, and a newly developed digital engine control system were crucial in meeting program objectives. XA100’s advance technologies and adaptive modes allowed the XA100 engine to deliver 25% fuel efficiency resulting in a 30% range increase, 2X mission systems cooling, and 25% improvement in acceleration over the most advanced engines being produced today.
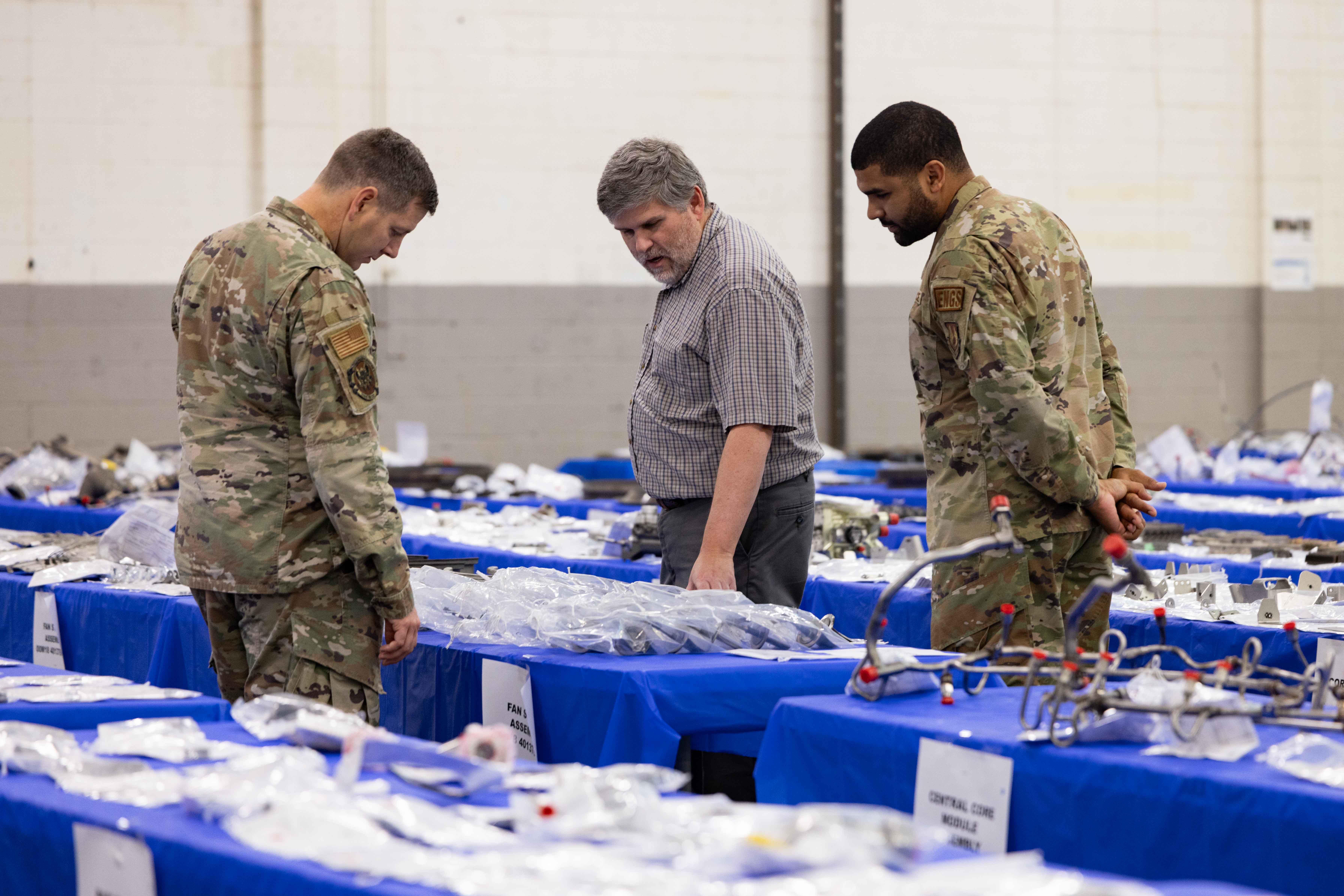
The rigorous campaign spanned two separate prototype engines that were tested in GE Aerospace’s high altitude test chamber in Ohio, as well as the USAF’s world-class Arnold Engineering Development Complex (AEDC) in Tennessee.
The experience in the control room was intense, Comer noted. “It’s completely silent, like you’re at a library. You’ve got several dozen people all glued to monitors, watching their part’s data at different simulated flight situations — at idle, full power, afterburner, and everything in between.”
All told, Comer said the XA100 team not only achieved the performance requirements but also worked with the government to achieve additional test hours to secure critical data to support future engine development. They ran prototype engines for hundreds of hours. That’s a rarity for a prototype, but all those test hours had a critical purpose. “Our team and the Air Force really maximized the value of testing to reduce future risk. We weren’t happy with just firing the engine up — we set out to hit every technical milestone, and we did,” she said. “We know the technology inside and out now. It’s not theoretical. It’s the real deal.”
The successful test campaign was part of the U.S. Air Force’s Adaptive Engine Transition Program (AETP), which was recently recognized by Aviation Week with a Laureate Award in the Defense category. This achievement by the GE Aerospace AETP team paves the way for future variable-cycle powerplants.
Up Next: The XA102
With the efforts of the XA100 test campaign now complete and showing such positive results, GE Aerospace is focusing its efforts on the next iteration of the adaptive cycle engine — the XA102, which is under development through the Air Force’s Next Generation Adaptive Propulsion (NGAP) program.
GE Aerospace recently announced completion of the XA102’s Detailed Design Review (DDR) with the Air Force, a major milestone on the road toward fielding the engine. The announcement came shortly after the Department of Defense awarded GE Aerospace a contract modification to continue advancing the engine toward prototyping as part of the NGAP program.
Unique to the XA102 program is the use of model-based systems engineering (MBSE), which is a revolutionary shift in the propulsion system design. In fact, it’s the first engine in company history to use the MBSE approach and was “instrumental in the success of the XA102 engine design,” said Steve “Doogie” Russell, vice president and general manager of Edison Works, the advanced defense products division of GE Aerospace.
Hundreds of engineers and support staff are hard at work developing the XA102 now, building on the deep engineering, manufacturing, and testing knowledge gained from the XA100’s strong performance.
“XA100 laid the foundation for XA102,” says Jorge Perez, general manager of advance combat engines. “All of our learnings will take it to the next level with significantly reduced risk and ensure we deliver an even better, more cost-effective solution for our customer at the pace they need it.”